-
29 W. Pawnee, Bloomfield, NJ 07003
What is Battery Cell Sorting, Why is it Required, and How to Do It?
Battery cell sorting represents a fundamental quality control process in lithium-ion battery manufacturing. This critical procedure involves categorizing individual cells based on their electrical parameters—including voltage, capacity, and internal resistance—to ensure optimal performance in assembled battery packs. Despite advanced manufacturing techniques, inherent variations among cells necessitate this sorting process to maintain consistency, safety, and longevity in battery applications.
Research indicates that even small differences between cells can significantly impact overall battery pack performance. According to industry standards, professionally sorted cells can extend battery lifespan by 15-20% and improve safety metrics by reducing thermal variance during operation. This article examines the technical aspects, methodologies, and importance of battery cell sorting in modern energy storage solutions.
What is Battery Cell Sorting?
Battery cell sorting is the systematic process of categorizing individual battery cells based on their specific electrical characteristics, including voltage, capacity, and internal resistance. We’ve discovered through years of experience that no two battery cells are exactly identical due to inherent manufacturing variations. These slight differences can significantly affect the overall performance of a battery pack when cells are grouped together.
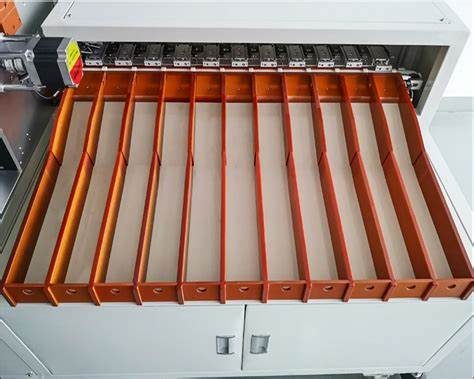
Cell sorting ensures only batteries with similar performance profiles work together in the same pack. This careful matching process is fundamental to creating balanced, efficient, and safe battery systems. We take pride in using advanced sorting technologies at VADE Battery to deliver consistent performance across our entire product range, from 18650 cells to custom LiFePO4 battery packs.
Why is Battery Cell Sorting Required?
The necessity for cell sorting stems from the unavoidable variability in battery manufacturing processes. Even with rigorous quality control measures, individual cells will exhibit differences in their electrical characteristics. Let’s explore why sorting is absolutely essential in professional battery pack production.
Performance Consistency
When we combine cells with varying capacities in a single battery pack, the result is an imbalanced system that drastically reduces efficiency and reliability. A battery pack’s performance is typically limited by its weakest cell – much like a chain is only as strong as its weakest link. By grouping cells with similar capacities and internal resistances, we ensure uniform power output and consistent performance throughout the battery’s life cycle.
Enhanced Safety
Safety is our top priority at VADE Battery. Properly sorted cells significantly reduce the risk of dangerous conditions like overheating, overcharging, and thermal runaway. Batteries with similar internal resistance generate heat more evenly during charge and discharge cycles, minimizing hot spots that could lead to catastrophic failures. This is particularly important in high-drain applications where energy density and power requirements are substantial.
Extended Battery Life
Battery packs made with properly sorted cells demonstrate significantly longer operational lifespans. When cells with similar aging characteristics are grouped together, they degrade at comparable rates, preventing premature failures that would otherwise require early replacement of the entire pack. This advantage is especially valuable in custom battery applications where reliability and longevity are critical factors.
Optimized Energy Output
Cell sorting ensures maximum energy utilization in every battery pack we manufacture. By matching cells with similar characteristics, we minimize energy losses and maximize the available capacity. This optimization is crucial for applications requiring stable performance, from electric vehicles to renewable energy storage systems. Our customers benefit from more consistent discharge curves and predictable performance in their specific applications.
How to Perform Battery Cell Sorting
At VADE Battery, we employ sophisticated processes and equipment to ensure precise cell sorting. Understanding this process helps our customers appreciate the quality built into every battery pack we deliver.
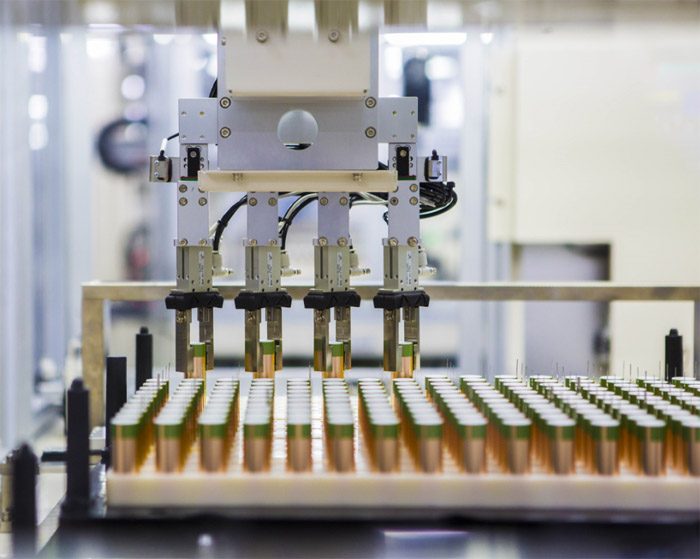
Cell Receiving and Inspection
The sorting process begins with thorough inspection of incoming cells for any physical defects or damage. Visual inspection helps identify obvious flaws before the cells undergo electrical testing. This initial screening ensures only physically sound cells proceed to the next stages of evaluation.
Electrical Testing
Each cell undergoes comprehensive electrical testing to measure critical parameters. State-of-the-art equipment precisely measures open circuit voltage (OCV), internal resistance (IR), and capacity. These measurements must meet exacting standards, as they determine the cell’s performance characteristics in real-world applications.
Data Acquisition and Analysis
Advanced sorting systems collect and analyze the measured data to determine each cell’s performance profile. Modern equipment can process thousands of cells per hour, ensuring efficient production while maintaining precision. The collected data forms the basis for classification decisions in the next step.
Sorting and Binning
Based on the analysis results, cells are automatically sorted into different bins according to predefined criteria. Modern sorting machines feature multiple channels (typically 5-20) to accommodate various classification levels. This automated process ensures cells with similar characteristics are grouped together for subsequent battery pack assembly.
Traceability Implementation
We implement robust data recording systems to maintain traceability for every cell in our production process. Barcode scanning and database management enable us to track each cell’s history and characteristics throughout its lifecycle. This traceability is invaluable for quality control and continuous improvement of our manufacturing processes.
Advanced Battery Cell Sorting Technologies
The technology behind cell sorting continues to evolve rapidly. At VADE Battery, we stay at the forefront of these advancements to deliver the highest quality products.
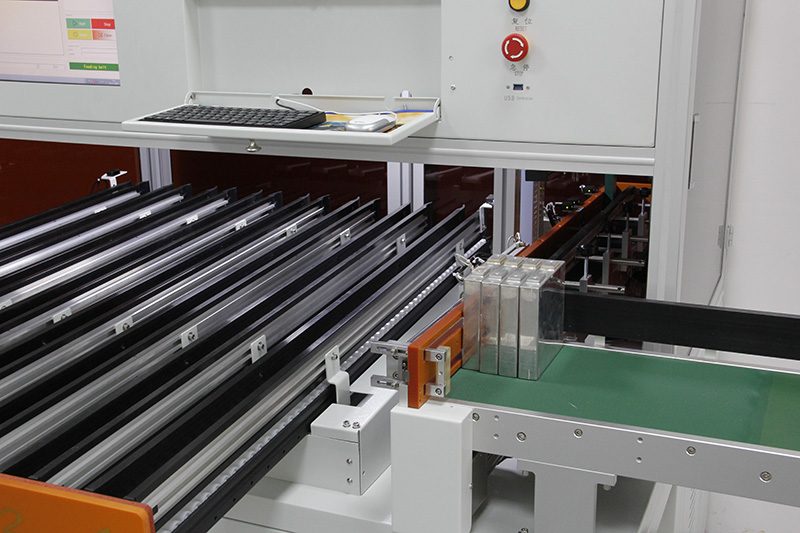
High-Precision Testing Equipment
Modern sorting machines utilize high-precision testing equipment like HIOKI internal resistance testers to achieve exceptional accuracy. These sophisticated instruments can detect minute differences between cells that would be impossible to identify through manual testing. The precision of these measurements directly impacts the quality of the final battery packs.
Automated Sorting Systems
State-of-the-art automated sorting systems have revolutionized battery manufacturing. These systems can process up to 2000 cells per hour while maintaining accuracy rates above 99.99%. Automation not only increases throughput but also dramatically reduces human error in the sorting process.
Multi-Parameter Analysis
Advanced sorting technologies now enable multi-parameter analysis for more precise cell characterization. By simultaneously evaluating multiple electrical characteristics, these systems can create more finely tuned groupings of cells. This sophisticated analysis leads to better-matched cells and superior performance in the final battery packs.
The Impact of Cell Sorting on Battery Applications
The benefits of proper cell sorting extend across numerous battery applications, from e-bikes to energy storage systems. Let’s examine how this critical process affects different use cases.
Electric Vehicle Applications
In electric vehicles, properly sorted cells contribute to extended range, consistent acceleration, and improved overall performance. The uniformity of cell characteristics helps optimize the battery management system’s effectiveness and extends the useful life of the expensive battery pack. This is particularly important as we move toward greater electrification of transportation.
Energy Storage Systems
For stationary energy storage applications, cell sorting ensures reliable performance and longer service life. These systems often operate for many years, making initial cell matching crucial for maintaining consistent performance throughout their operational lifetime. The economic benefits of extended service life make thorough cell sorting a wise investment.
Portable Electronics
Even in smaller applications like portable electronics, cell sorting plays a vital role in delivering consistent performance. Products using our lithium polymer batteries benefit from extended runtime and more reliable operation due to our meticulous sorting processes. The difference becomes particularly noticeable as devices age.
Why Choose VADE Battery for Your Custom Battery Needs
At VADE Battery, we specialize in creating custom rechargeable18650, Li-ion, Lithium polymer, and LiFePO4 battery packs for customers worldwide. Our rigorous cell sorting processes ensure every battery pack we produce delivers exceptional performance, safety, and longevity.
We understand the components of lithium-ion battery packs intimately and implement best practices in our custom battery manufacturing process. Our commitment to quality extends from initial cell selection through final pack assembly and testing.
Whether you’re looking for high-drain 18650 cells or complete custom battery solutions, we have the expertise to deliver products that exceed your expectations. Our thorough understanding of series and parallel battery configurations ensures optimal performance for your specific application.
Conclusion
Battery cell sorting stands as a crucial quality assurance process in the lithium-ion battery production chain. The evidence presented throughout this article demonstrates how proper cell matching directly influences performance consistency, safety parameters, and operational lifespan of battery packs across applications.
As battery technology continues to evolve, sorting methodologies are similarly advancing—from basic voltage measurements to sophisticated multi-parameter algorithms that can detect subtle variations between seemingly identical cells. These advancements will likely continue to drive improvements in battery performance metrics while reducing costs through optimized resource utilization and extended service life.
Battery manufacturers and integrators who implement rigorous sorting protocols position themselves to deliver superior products that meet increasingly demanding technical specifications. For professionals seeking to optimize battery performance, understanding the principles and technologies behind cell sorting provides valuable insight into a critical quality control process that shapes the future of energy storage solutions.