-
29 W. Pawnee, Bloomfield, NJ 07003
Cómo nace una batería VADE de alta calidad
Como Ingeniero Jefe de Producción en VADE Battery, con más de 15 años de experiencia en el sector, me enorgullece presentar nuestro proceso de fabricación patentado de 12 pasos, que distingue a nuestras baterías. En VADE, nos especializamos en soluciones de baterías recargables personalizadas desde 2008, entregando más de 5 millones de unidades de baterías 18650, de iones de litio, de polímero de litio y LiFePO4 a clientes en 43 países de todo el mundo. Nuestras baterías alcanzan constantemente una tasa de fiabilidad de 99,71 TP3T y una vida útil 251 TP3T superior a la media del sector, gracias a nuestro meticuloso control de calidad y a nuestras avanzadas técnicas de producción.
La Fundación: Materiales de primera calidad
En primer lugar, obtenemos nuestras celdas de batería y placas de protección de proveedores externos. Las baterías VADE utilizan celdas de proveedores de marcas de primer nivel: la misma calidad que las baterías originales de Apple. Nuestras placas de protección implementan soluciones de Texas Instruments (TI), lo que garantiza su pleno funcionamiento incluso después de las actualizaciones del sistema iOS.
El nacimiento de la excelencia: nuestro proceso de fabricación de 12 pasos
Inspección de materiales
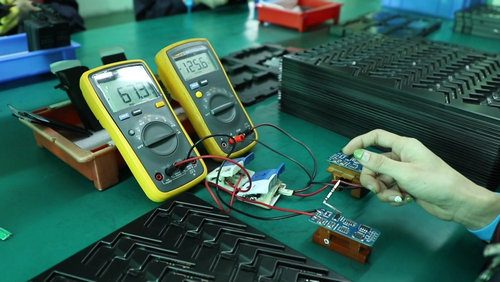
Todos los materiales adquiridos se someten a una rigurosa inspección de entrada con equipos especializados para verificar las especificaciones y los parámetros de calidad. Los materiales de baja calidad se rechazan de inmediato, lo que constituye la primera barrera crítica de control de calidad en nuestro proceso de producción. Esta inspección incluye la verificación de la composición química, las propiedades físicas y la precisión dimensional.
Clasificación de la capacidad de las celdas de la batería
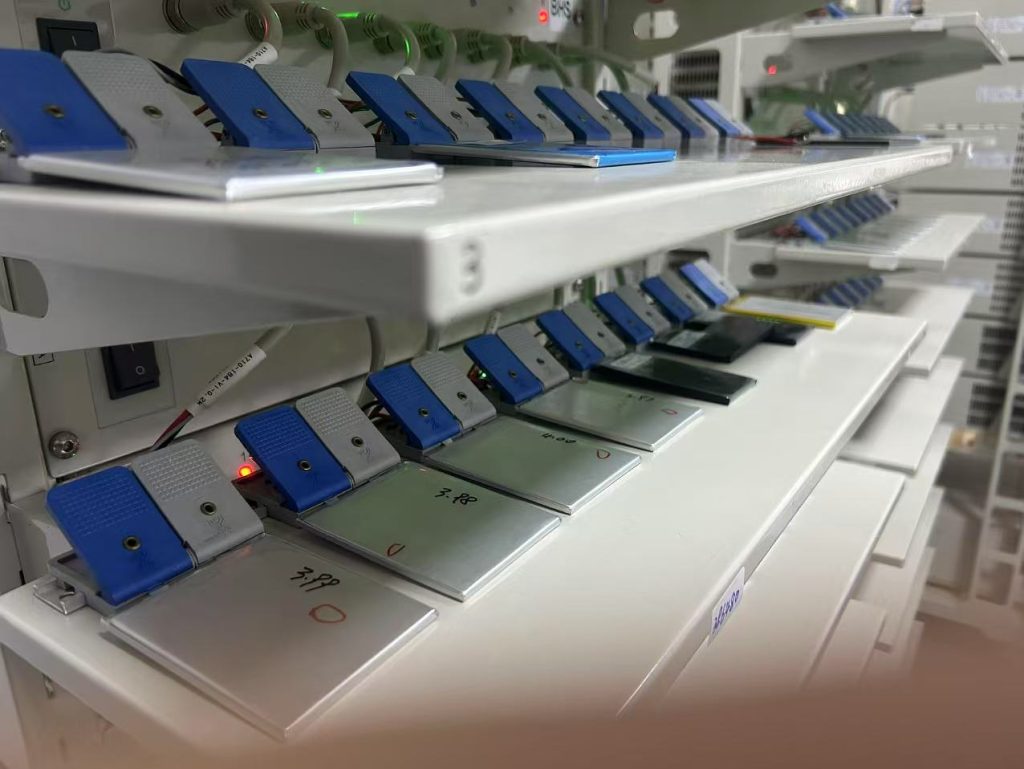
Las celdas de batería se someten a un proceso de clasificación por capacidad, conocido en la industria como "formación". En VADE, operamos 15 cabinas de clasificación capaces de procesar simultáneamente hasta 12 000 baterías. Esta activación electroquímica forma la interfase de electrolito sólido (ISE) en el ánodo durante los ciclos iniciales de carga y descarga, lo que garantiza un rendimiento uniforme en todos nuestros productos.
Carga celular automatizada

Tras la inspección y clasificación, las celdas entran en nuestra línea de producción automatizada. Mediante robótica de precisión y sistemas de transporte, cada celda se posiciona con precisión para su posterior procesamiento. Esta automatización minimiza los errores humanos y los riesgos de contaminación, a la vez que maximiza la eficiencia del proceso.
Corte de lengüetas de níquel

A continuación, se realiza el corte de precisión de las lengüetas de níquel. Estas tiras metálicas conductoras deben recortarse según las especificaciones exactas (ni demasiado largas ni demasiado cortas) para garantizar las conexiones eléctricas correctas dentro de la batería. La avanzada tecnología de corte láser mantiene tolerancias micrométricas, esenciales para un rendimiento y una seguridad óptimos.
Soldadura por puntos láser

Este paso crítico une la placa de protección a la celda de la batería mediante soldadura láser por puntos. Nuestro equipo de alta precisión crea uniones moleculares entre los componentes, minimizando las zonas afectadas por el calor y maximizando la resistencia de la conexión y la conductividad eléctrica. Estas soldaduras se someten a pruebas de integridad mecánica y resistencia eléctrica.
Aplicación de aislamiento

Aplicamos un adhesivo aislante especializado para proteger los cables y conexiones expuestos, previniendo posibles cortocircuitos. Este material dieléctrico proporciona un aislamiento eléctrico esencial a la vez que mantiene la estabilidad térmica en diversas condiciones de funcionamiento, lo que reduce significativamente los riesgos de seguridad.
Instalación del soporte

Esta etapa requiere la operación manual de nuestros técnicos cualificados. Durante la instalación de los soportes estructurales, nuestro personal realiza simultáneamente inspecciones visuales de los procesos automatizados previos, lo que añade un nivel adicional de control de calidad. Esta supervisión humana complementa los sistemas automatizados, detectando defectos sutiles que las máquinas podrían pasar por alto.
Aplicación de papel protector para la cabeza

Aplicamos un papel protector especializado para cubrir el cabezal de la batería. Este material multifuncional proporciona protección mecánica y aislamiento eléctrico, mejorando tanto la estética como la seguridad operativa. El material está dimensionado y colocado con precisión para garantizar la cobertura completa de los componentes sensibles.
Pruebas de rendimiento

Cada batería se somete a pruebas exhaustivas de rendimiento con equipos calibrados para medir parámetros críticos como el voltaje, la resistencia interna, la capacidad, la tasa de autodescarga y el rendimiento del ciclo. Solo las baterías que cumplen con nuestras estrictas especificaciones pasan a la siguiente etapa; las demás se separan para su análisis y reciclaje.
Inspección de apariencia

Nuestro equipo de control de calidad realiza meticulosas inspecciones visuales para detectar defectos físicos como abolladuras, deformaciones o rayones. Este protocolo de inspección 100% emplea técnicas de examen directo y de aumento para identificar incluso imperfecciones microscópicas que podrían afectar el rendimiento o la seguridad.
Detección de fugas de presión

Utilizamos equipos avanzados de detección de fugas con presión positiva que identifican defectos imperceptibles que pueden causar hinchazón o problemas térmicos en la batería. Esta tecnología aplica presión controlada a la batería sellada, a la vez que monitorea los cambios de presión que podrían indicar fugas microscópicas, lo que mejora significativamente la seguridad.
Embalaje y envío
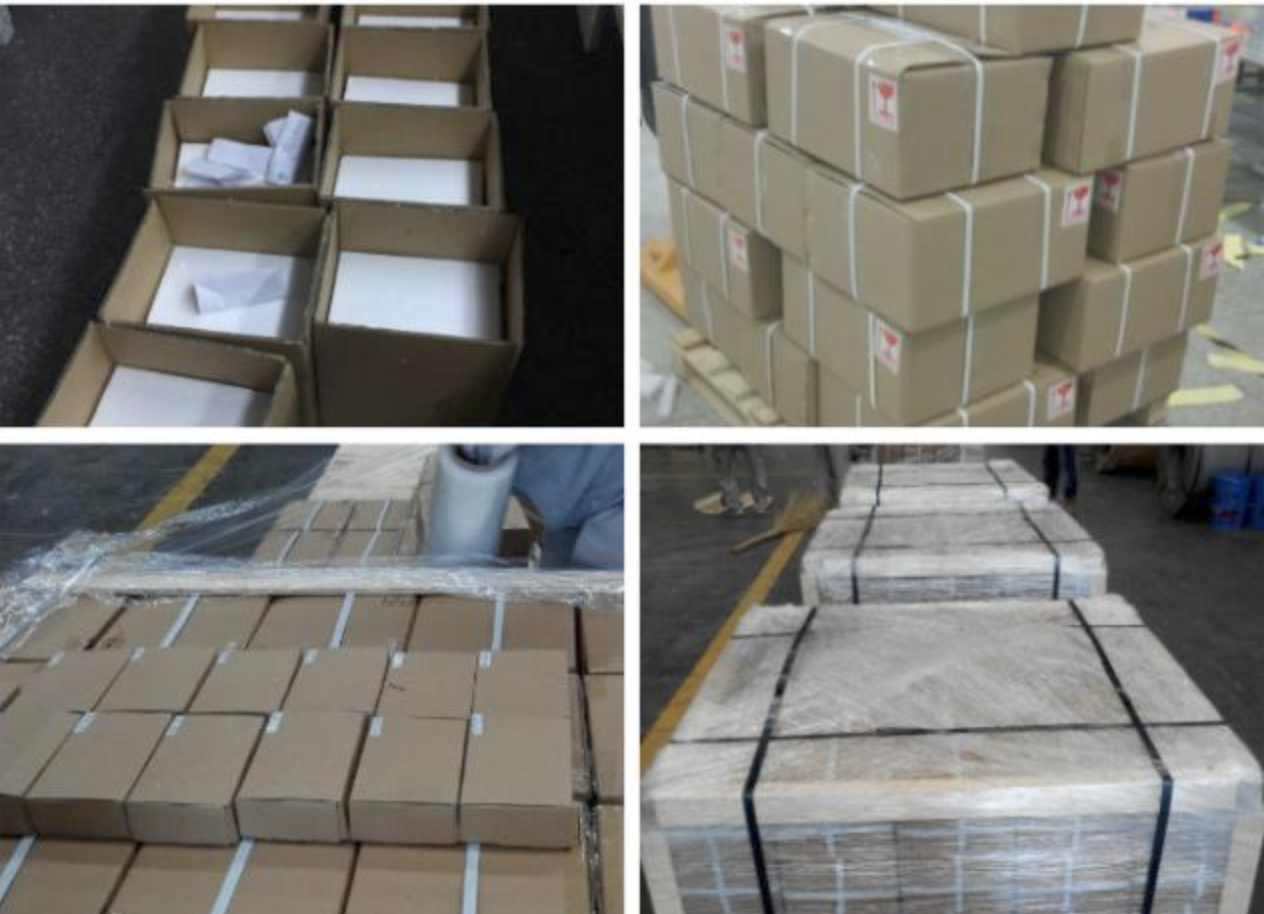
Las baterías aprobadas se empaquetan cuidadosamente según las normas internacionales de seguridad para el transporte de baterías de litio. Cada batería se coloca en blísteres de diseño personalizado con protección contra impactos, se sella en cajas de venta al público con precinto de seguridad y se empaca en cajas de envío con certificación de la ONU que cumplen con la normativa internacional sobre materiales peligrosos.
La promesa de calidad de VADE
Cada batería VADE se somete a este riguroso proceso de fabricación antes de salir de nuestra fábrica con certificación ISO 9001:2015 y UL. Nuestro sistema de control estadístico de procesos mantiene una tasa de defectos inferior a 0,31 TP3T, superando con creces el promedio del sector de 1,21 TP3T. Respaldamos nuestros productos con una garantía integral de 24 meses, el doble del estándar del sector.
Nuestro compromiso con la excelencia va más allá del rendimiento y abarca la sostenibilidad. En 2024, redujimos nuestra huella de carbono de fabricación en 351 TP3T mediante la modernización de equipos de bajo consumo y el abastecimiento responsable de materiales. Nuestro programa de reciclaje de baterías ya ha procesado más de 500.000 unidades, recuperando 921 TP3T de materiales valiosos.
Desde nuestros materiales que cumplen con las normas RoHS y REACH hasta nuestros protocolos de seguridad con certificación IEC 62133, priorizamos la calidad, la seguridad y la responsabilidad ambiental en cada batería que fabricamos. Nuestros clientes, incluidos fabricantes líderes de dispositivos médicos, proveedores de automoción y marcas de electrónica de consumo, confían en las baterías VADE cuando la fiabilidad es fundamental.
Para conocer especificaciones detalladas sobre nuestras tecnologías de baterías, descargue nuestros documentos técnicos en Conceptos básicos de las baterías de iones de litio o explore nuestra selección de procesos de fabricación de baterías de litio personalizados. Contacte con nuestro equipo de ingeniería hoy mismo para discutir sus requisitos específicos de batería.